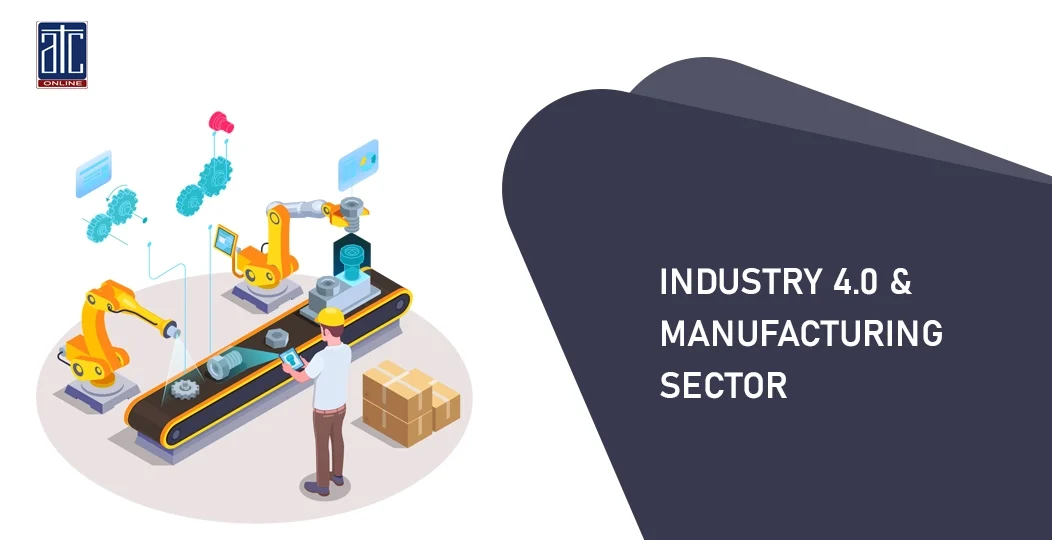
Industry 4.0 is an evolution of the industrial sector that uses advanced technologies such as the Internet of Things (IoT), big data, artificial intelligence (AI) and robotics to create a more interconnected, automated, and intelligent manufacturing environment. This new industrial revolution, also known as the fourth industrial revolution. Industry 4.0 is expected to revolutionize the manufacturing sector, enabling greater automation and increased efficiency. Additionally, the use of these technologies can reduce the environmental impact of production processes and help manufacturers become more competitive.
Industry 4.0 enhances connectivity and analytics to empower manufacturers to make more informed decisions, help mitigate risks, and identify potential problems before they occur. Also, Industry 4.0 will enable manufacturers to have greater visibility into the entire production process, allowing them to better manage and optimize resources, while providing customers with more personalized products. Let us now understand in some detail, how the elements of Industry 4.0 will impact the Manufacturing Sector.
INTERNET OF THINGS

The Internet of Things (IoT) is revolutionizing the manufacturing industry. IoT technology enables manufacturers to gather real-time data from connected sensors throughout their supply chain, allowing them to monitor and control production in a more efficient and cost-effective manner. IoT technology also helps manufacturers reduce downtime, improve production processes, and optimize energy usage. Additionally, IoT-enabled products can be tracked throughout their lifecycle, allowing manufacturers to better understand customer needs. By connecting machines, products, and people, the IoT is making the manufacturing industry more automated, efficient, and profitable.
CYBER-PHYSICAL SYSTEMS

Cyber-Physical Systems (CPS) are a category of technology that connects physical components like equipment and sensors to an information system via wireless or wired connections. This link allows the physical components to be controlled and monitored remotely and in real time. CPS is used in the manufacturing industry to boost efficiency, save costs, and improve safety.
CPS can monitor and operate industrial machinery like robots and conveyor belts. This can assist guarantee that equipment are running correctly and in the most effective manner feasible. Sensors and other technologies can be used to identify machine flaws and notify workers to possible problems in some circumstances. Furthermore, CPS may be used to track machine performance, allowing manufacturers to find areas where their processes can be improved.
Cyber-Physical Systems may also be used to gather machine data and analyze it for insights that might help firms improve their manufacturing processes. This information may be utilized to spot patterns, cut waste, and improve output. Furthermore, CPS can offer real-time notifications when machines are not performing as planned, allowing manufacturers to take remedial action as soon as possible.
CPS can thus, transform production, allowing manufacturers to enhance productivity while decreasing costs. This technology will become more extensively employed in manufacturing industries as it advances, allowing for even larger cost reductions and efficiency benefits.
BIG DATA ANALYTICS

Big Data Analytics is the process of analyzing large and complex data sets to uncover patterns, correlations, and other insights. It involves the use of advanced analytics techniques, such as machine learning, artificial intelligence, predictive analytics, and statistical analysis, to gain insights from data that can be used to make better decisions.
Big Data Analytics can have a major impact on the manufacturing sector by enabling manufacturers to improve the efficiency and effectiveness of their operations. By leveraging data from sensors, machine logs, and other sources, manufacturers can gain insights into their production process and identify areas of improvement. With better visibility into their operations, manufacturers can optimize their production schedules, reduce costs, and increase productivity. Additionally, Big Data Analytics can be used to identify and address quality issues, detect abnormalities, and improve customer service. Ultimately, Big Data Analytics can help manufacturers become more competitive, improve their bottom line, and maintain their competitive edge.
ARTIFICIAL INTELLIGENCE

Artificial Intelligence (AI) is an area of computer science that emphasizes the creation of intelligent machines that work and react like humans. AI involves the study and use of algorithms, machine learning, natural language processing, and robotics to develop systems that can perceive their environment and take actions to achieve specific goals. It is also commonly used to refer to machines that mimic cognitive functions associated with the human mind, such as learning and problem-solving.
Artificial Intelligence (AI) is being used increasingly in the manufacturing industry. AI can help manufacturing companies to increase efficiency, reduce costs, and improve quality. It can be used to automate production processes, monitor production lines, detect defects in products, and optimize production schedules. AI can be employed to analyze customer data and optimize marketing campaigns. AI is also being increasingly used to develop predictive models for predicting demand for products. Also, Artificial Intelligence has its use in automating customer service processes to provide personalized customer experiences. This technology is also being used to develop new products and services, and to optimize supply chain operations. AI is an invaluable tool for manufacturers, and its use is likely to increase in the future.
AUGMENTED REALITY

Augmented reality (AR) is a technology that layers computer-generated enhancements atop an existing reality in order to make it more meaningful through the ability to interact with it. AR enhances one’s current perception of reality, whereas in contrast, virtual reality replaces the real-world environment with a simulated one. Augmented reality can be experienced through devices such as smartphones, tablets, smart glasses, and head-mounted displays.
AR may be used in manufacturing to develop, build, and manage goods in a more efficient and cost-effective manner. AR may be utilized for visualization, improved understanding of the assembly process, real-time feedback on machine performance, and diagnosing and repairing equipment in difficult-to-reach locations. Some of the advantages of using AR in manufacturing include:
- Improved Efficiency: AR can help streamline the manufacturing process by providing users with real-time information and feedback on the performance of machines and equipment. This can help reduce downtime and improve efficiency.
- Cost Savings: AR can help reduce the cost of manufacturing by providing an efficient way to design, build, and maintain products.
- Improved Safety: AR can provide workers with better visibility when working in difficult-to-reach places, reducing the risk of injury and accidents.
- Increased Productivity: AR can help workers to quickly identify and troubleshoot problems, resulting in improved productivity and reduced downtime.
3-D PRINTING

3-D printing, also known as additive manufacturing, is a process of making three dimensional solid objects from a digital file. The creation of a 3D printed object is achieved using additive processes. In an additive process an object is created by laying down successive layers of material until the entire object is created. Each of these layers can be seen as a thinly sliced horizontal cross-section of the eventual object. 3-D printing is the opposite of subtractive manufacturing which is cutting out / hollowing out a piece of metal or plastic with for instance a milling machine.
3-D printing is a revolutionary technology that has already made its mark in manufacturing processes. It is a relatively new way of producing parts and components for a variety of industries, including automotive, aerospace, medical, and consumer products. One of the benefits of using this technology in manufacturing is that it allows for rapid prototyping. This means that a design can be tested quickly and efficiently, allowing designers to make changes to the design without having to start from scratch. It also eliminates the need for costly tooling, which can take months to produce.
The 3-D printing also offers a great degree of customization, allowing manufacturers to produce parts that are tailored to the exact specifications of their customers. This can help to reduce manufacturing costs, as well as speed up production times. Finally, 3-D printing is becoming increasingly popular for producing end-use parts. By printing parts on-demand, manufacturers can reduce their inventory costs and increase their agility. This can help them to stay ahead of their competition, as well as get their products to market faster. Thus, by leveraging the power of this technology, manufacturers can reduce costs, increase efficiency, and gain a competitive edge.
AUTONOMOUS VEHICLES

An autonomous vehicle is a vehicle that can sense its environment and navigate without human input. Autonomous vehicles use a variety of techniques to detect their surroundings, such as Radar, Lidar, GPS, and computer vision. They can operate in a range of driving scenarios from highways to urban streets.
Autonomous vehicles are increasingly being used in the manufacturing industry to reduce costs and increase efficiency. Such vehicles can be used to transport goods between different parts of a factory or warehouse, eliminating the need for manual labor. Additionally, they can be used to transport parts and materials throughout the production line, allowing for faster production times. Autonomous vehicles can also be used to monitor production processes, ensuring quality control. Finally, autonomous vehicles can be used for safety purposes, such as patrolling the factory or warehouse to detect potential hazards.
ROBOTICS

Robotics is the science and engineering of designing, constructing, and operating robots. It involves the use of machines and algorithms to complete tasks that are typically too difficult or dangerous for humans to perform. It is a multidisciplinary field that draws from a variety of disciplines, including computer science, electrical engineering, mechanical engineering, and artificial intelligence. Robotics is used in many industries, from manufacturing and automation to medical, space exploration, and consumer products. It is a rapidly growing field with significant potential for future applications.
Robotics is increasingly being used in manufacturing to enhance efficiency, accuracy, and safety. Robots are used in many applications such as material handling, welding, assembly, painting, packaging, and palletizing. They can work in hazardous environments and help to reduce fatigue, repetitive strain injuries, and worker absenteeism. In addition, robotic systems are able to work much faster than human workers, enabling improved production throughput and efficiency. Robotics also has the potential to reduce lead times and increase product quality. As robots become more intelligent and efficient, they are expected to play a major role in the future of manufacturing.
FINAL THOUGHTS
Industry 4.0 is transforming the traditional manufacturing industry with the introduction of smart factories and new technologies. These technologies include Internet of Things, artificial intelligence, and advanced robotics, to name a few. This new industrial revolution is creating factories that are more connected, automated, and efficient than ever before. Industry 4.0 is revolutionizing the manufacturing process, leading to faster production, improved quality control, and greater cost savings. It is also allowing manufacturers to customize products more quickly and efficiently, and create new products with greater accuracy and speed. By leveraging the power of Industry 4.0, manufacturers can remain competitive in the global market and stay ahead of the curve.
PACIFYCA by ATC ONLINE is a comprehensive automation software solution (ERP) for the contemporary manufacturing sector. Our ERP solution is a future-ready, yet easy, one-point integrated platform that synchronizes all important organizational entities. For more information on PACIFYCA ERP, visit us at: www.atconline.biz
You could also contact us at https://atconline.biz/contact/ for business enquires and product information.